Epoxy Ink Packet Mixing Instruction: The 12.5 Gram Packet contains precisely weighed portions of ink and catalyst, 12 grams of ink and 5 grams of catalyst.
(1). Remove the plastic clip.
(2). Mix the two parts together thoroughly, allowing an introduction period of around 30 minutes or so.
(3). Cut off one of the corners of the package and dispense the ink onto a glass or metal plate.
(4). The glass plate will become your stamp pad/Inking Plate.
(5). Use a hard rubber ink roller rolling the ink into a very thin film onto the glass.
(6). Your ready to start marking parts with a rubber stamp, band stamp or any other related marking device.
PROPERTIES: A two-phase epoxy ink characterized by a high degree of adhesion to a variety of “difficult” surfaces such as ceramics, phenolic, polyesters, melamine, silicones as well as ferrous and non-ferrous metals and glass. They exhibit excellent resistance to solvents and chemicals has excellent opacity.
When using these inks always use clean equipment for the mixing of colors and be sure that the surface to be printed is clean and free of grease and dirt. Improperly cleaned surfaces may result in imperfections in the ink film. These may take the form of craters or crawling of the ink. If this problem is encountered the surface should be cleaned with alcohol to insure the removal of grease and dust.
APPLICATIONS: Used for part marking in the aerospace, automotive, appliance, electronics, glass and ceramic industries. Designed to be used with rubber stamps and on offset printers and other related marking devices.
MIL SPECS: MIL-I-43553, MIL STD-202e, MIL-STD-810c, MIL-STD-1285a, A-A-56032a, A-A-56032c, A-A-56032d.
COLORS: Black and White.
OTHER COLORS: Quarts offer more options with other colors; Brown, Green, Blue, Red, Orange, Yellow, Burgundy and custom colors.
CURE CYCLES: Drying: By polymerization. These inks require the addition of a catalyst immediately prior to use. Air dry from 2 to 3 hours but 7
to 10 days are required for maximum adhesion and chemical resistance.
Curing recommended as follows: 180F Degrees = 30 minutes; 250F Degrees = 10 minutes; 300F Degrees = 7 minutes; 320F Degrees = 4 minutes.
POT LIFE: Under normal conditions, one to two hours after the two components are mixed. Higher than normal room temperatures will shorten Application of a small amount of Epoxy Thinner when ink dries to fast will prolong transferability.
SHELF LIFE: Use within one year is suggested. Best to refrigerate before and after using unused portion.
PACKAGING: The 12.5 Gram Packet contains precisely weighed portions of ink and catalyst, 12 grams of ink and 5 grams of catalyst.
THINNER/CLEANER: Epoxy Thinner available in quarts and gallons.
RETARDENT: If ink is drying to fast merly add a few drops of retardent. Available in Pints and quarts.
SAFETY & MEDICAL INFO: Combustible - Flash point 142F Degrees. Emergency First Aid - Skin contact, wash well with soap and water. Eyes flush with water. WARNING! Vapor may cause eye respiratory irritation. Eye or skin contact may cause irritation. Repeated and prolonged overexposure by inhalation or skin absorption may cause kidney, liver and blood damage. induce vomiting, call doctor immediately. Contains lead and chromates and the physician should be so advised.
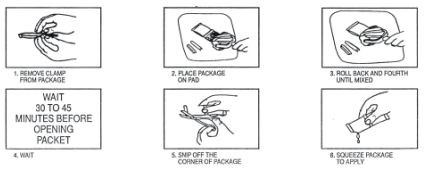
Questions or comments call us at 323-582-6461 or email us at info@HPRubberStamp.com